Mastering Shipping Container Transportation for U.S. Trade: 5 Essential Steps
In today’s global trade environment, over 90% of international cargo is transported via container shipping. With the U.S. implementing new Container Security Initiative (CSI) protocols and stricter customs regulations in 2023, businesses must understand the logistics behind shipping containers to ensure smooth operations. Whether you are a small exporter or a large manufacturer, mastering cost optimization, compliance, and risk management in container transportation can directly impact your competitiveness. This guide breaks down five essential steps to help you efficiently manage U.S. import logistics, from selecting containers to customs clearance.
Related searches
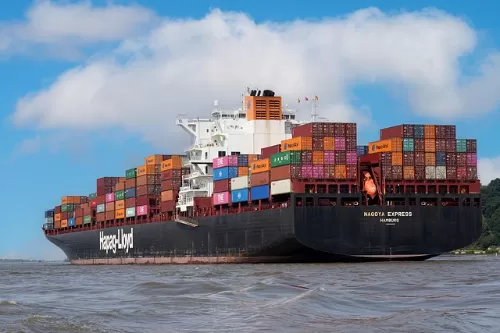
Choosing the Right Shipping Container
Selecting the correct container type is the first step in efficient transportation. The most commonly used container types include:
Standard Dry Containers (20FT & 40FT) – Suitable for general goods.
Refrigerated Containers (Reefers) – Required for food and pharmaceuticals.
Open-Top & Flat-Rack Containers – Ideal for oversized cargo.
U.S.-Specific Regulations to Note:
All containers must comply with ISO 6346 international standards.
Food shipments require USDA-certified refrigerated containers.
Wood packaging materials must be heat-treated per ISPM-15 standards.
Pro Tip: First-time exporters should start with trial shipments using 20FT containers to minimize risks and test logistics reliability.
Packing & Transportation Optimization
Proper packing strategies help minimize costs and prevent cargo damage. Follow these best practices:
For heavy machinery: Place heavier items near the container door for balanced weight distribution.
For fragile goods: Use at least 15 cm of buffer space and secure cargo with airbags.
Weight distribution compliance:
Front-to-back weight difference should not exceed 3 tons.
Left-to-right deviation must be within 2 tons.
Choosing the Right Shipping Route:
West Coast Route (Shanghai → Los Angeles): 15-18 days transit, best for time-sensitive shipments.
East Coast Route (Shenzhen → New York): 25-30 days transit, typically 10-15% cheaper.
Gulf Coast Route (Ningbo → Houston): Lower port fees (20% savings) but fewer direct sailings.
2023 U.S. Customs Update: All inbound containers must be equipped with electronic seals—coordinate with your freight forwarder to ensure compliance.
Navigating U.S. Customs & Documentation
Clearing customs smoothly requires accurate documentation and compliance with U.S. regulations. The three key clearance stages include pre-declaration, port inspection, and final release.
Essential Documents for U.S. Import Clearance:
Commercial Invoice – Must include detailed HS codes.
Packing List – Specifies weight, volume, and quantity.
Bill of Lading (B/L) – Proof of shipment.
Certificate of Origin – Required for certain goods.
Product-Specific Certifications:
FDA approval for food, cosmetics, and drugs.
FCC certification for electronic products.
CPSC compliance for furniture and household goods.
Pro Tip: Prepare an “emergency document kit” containing supplementary materials to reduce clearance delays caused by customs inspections.
Cost Control & Risk Management
Shipping costs can be broken down into:
60% Ocean Freight、20% Inland Transportation、15% Port Charges、5% Other Fees
Cost-Saving Strategies:
LCL (Less than Container Load): Ideal for shipments between 5-15 CBM.
Long-term Contract Rates: More stable than spot rates.
Multimodal Transport: Rail + truck combinations can reduce last-mile costs.
Alternative Ports: Houston is 20% cheaper than Los Angeles for imports.
Risk Prevention Measures:
Cargo Insurance – Coverage should be at least 110% of cargo value.
Buffer Time – Allow 10-15 extra days for unforeseen delays.
Customs Broker Backup List – Always have alternative brokers for urgent situations.
Stay Updated – Regularly monitor U.S. customs policy changes to avoid non-compliance.
Handling Disputes & Unexpected Issues
Dealing with Demurrage & Port Delays
Ports in the U.S. often experience congestion, leading to extra storage fees (demurrage). To avoid these costs:
Pre-schedule trucking services before arrival.
Negotiate extended free storage time with carriers.
Use real-time tracking for proactive issue resolution.
What to Do in Case of Cargo Damage?
If cargo arrives damaged, take these steps immediately:
Photograph & Document Evidence.
Notify Insurance & Freight Forwarders.
Request an Independent Inspection Report.
File Claims within 3 Business Days.
Handling Trade War Tariffs & Compliance Issues
If your products are subject to high U.S. tariffs, consider:
Applying for Tariff Exemptions.
Reclassifying HS Codes to potentially reduce duties.
Transshipping through Third Countries to lower costs.
Conclusion
To optimize shipping container transportation for U.S. imports, take these key steps:
Standardize Packing Procedures for efficiency.
Partner with Reliable Freight Forwarders (work with at least 2-3 trusted agents).
Stay Updated on U.S. Customs Changes (attend regular briefings).
Train Your Logistics Team on compliance best practices.
By mastering these five essential steps, you can significantly reduce shipping risks, lower costs, and improve efficiency, strengthening your global trade competitiveness. In today’s fast-changing trade environment, a well-managed logistics system is your key advantage.